沂源優(yōu)質(zhì)機械制造廠家
發(fā)布時間:2021-12-25 10:45:42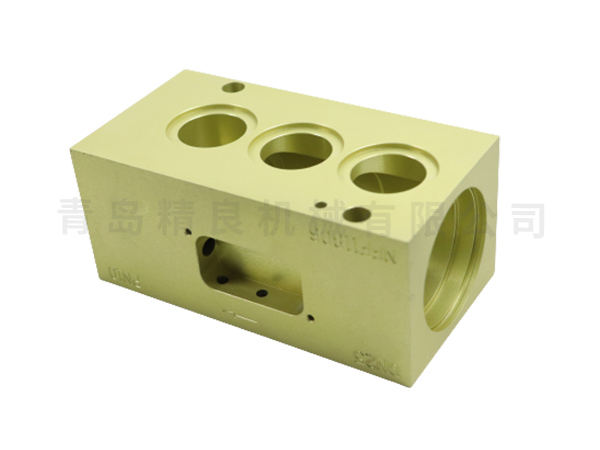
沂源優(yōu)質(zhì)機械制造廠家
4.機械零件常見的失效方式:因強度缺乏而開裂;過大的彈性變形或塑性變形;摩擦外表的過度磨損、打滑或過熱;銜接松動;容器、管道等的走漏;運動精度達不到規(guī)劃要求。5.應(yīng)力的分類:分為靜應(yīng)力和變應(yīng)力?;镜淖儜?yīng)力為安穩(wěn)循環(huán)變應(yīng)力, 安穩(wěn)循環(huán)變應(yīng)力有非對稱循環(huán)變應(yīng)力、脈動循環(huán)變應(yīng)力和對稱循環(huán)變應(yīng)力三種。疲憊損壞及其特點:變應(yīng)力效果下的損壞稱為疲憊損壞。特點:在某類變應(yīng)力多次效果后忽然開裂;開裂時變應(yīng)力的臨界應(yīng)力遠小于材料的屈從極限;即使是塑性材料,開裂時也無明顯的塑性變形。確認疲憊極限時,應(yīng)考慮應(yīng)力的大小、循環(huán)次數(shù)和循環(huán)特征。
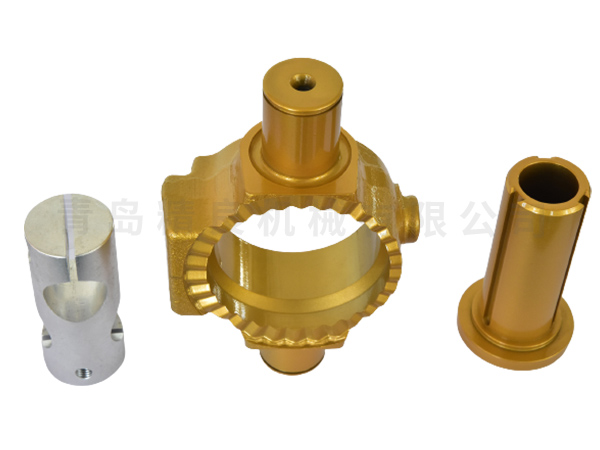
沂源優(yōu)質(zhì)機械制造廠家
數(shù)控車床加工較好地辦理了復(fù)雜、精 密、少數(shù)目、多種類的零件加工疑問,是一種柔性的、高效能的自動化機床,代表了當(dāng)代機床掌握技術(shù)的發(fā)展偏向,是一種典范的機電一體化產(chǎn)品。精 密數(shù)控車床出現(xiàn)故障以后要立刻對其進行檢驗,惟有找到癥結(jié)所在才氣夠?qū)ζ溥M行修理,一般來說對于車床進行疑問的檢驗具備的技巧或是非常多的,比方道理剖析法,但是當(dāng)這些方法都經(jīng)過應(yīng)用,而仍然不具備結(jié)果的時候就需求應(yīng)用到另外一種方法了,那即是器件互換法,平時情況下這種檢驗方法都是在末了才進行應(yīng)用的,再沒有其余方法以后接納器件互換法進行疑問故障排查所具備的結(jié)果,非常出色,能夠完善對疑問進行辦理,但是在這個歷程之中所花消的時間比較較多。

沂源優(yōu)質(zhì)機械制造廠家
首先,要會看圖紙,會看圖紙之后,桿依據(jù)零件特點分[ ]別類選擇性的給適合的供應(yīng)商下單,否則就會價格交期質(zhì)量全凌亂。(只是簡單的看懂,稍微懂圖紙的尺寸公役,形位公役,資料熱處理,技術(shù)要求的范圍等,這點 ,收購要具有基礎(chǔ)常識,將圖紙分類進行收購作。第二,會計算資料費用:(懂得零件的余量放法及毛坯的計算方法,這點要向老師傅學(xué)習(xí)和自己積累)第三,會排零件的加工工藝:(包括熱處理,特種加工的工藝等,不需要多會,只需知道產(chǎn)品大概加工步驟)

沂源優(yōu)質(zhì)機械制造廠家
(4)自動測量法:在加工過程中,邊加工邊丈量加工尺度,并將所測結(jié)果與設(shè)計要求的尺度比較后,或使機床繼續(xù)作業(yè) ,或使機床停止作業(yè),這便是自動丈量法。目前,自動丈量中的數(shù)值已可用數(shù)字顯示。自動丈量法把丈量設(shè)備加入工藝體系(即機床、刀具夾具和工件組成的統(tǒng)一體)中 ,成為其第五個因素。自動測量法質(zhì)量安穩(wěn)、出產(chǎn)率高 ,是發(fā)展方向。

沂源優(yōu)質(zhì)機械制造廠家
為了提高機械零件加工質(zhì)量,需要找出造成加工誤差的主要因素,這是關(guān)鍵,需要采取相應(yīng)的措施來減少或控制這些因素的發(fā)生。一、誤差分組法:該方法根據(jù)誤差大小將精加工或在線加工的工作尺寸分成n組,然后根據(jù)誤差范圍調(diào)整刀具相對于工件的位置。二、誤差補償法:這種方法的主要目的是創(chuàng)建新的原始誤差,抵消原始工藝系統(tǒng)固有的原始誤差,從而達到降低加工誤差和加工精度的目。三、誤差轉(zhuǎn)移法:該方法實質(zhì)上是將工藝系統(tǒng)的幾何誤差、 受力變形和熱變形等轉(zhuǎn)移到不影響加工精度的方向。例如,對于具有分級或轉(zhuǎn)級的多工位工序或采用轉(zhuǎn)級刀架加工的工序,其分級、轉(zhuǎn)級企業(yè)家誤差直接影響零件表面的加工精度。